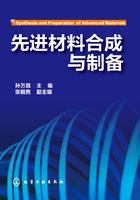
2.4 溶胶-凝胶法
2.4.1 溶胶-凝胶法的发展历程
溶胶-凝胶法制备薄膜的最初研究可追溯至1846年,Ebelnen首次研究了正硅酸乙酯在酸性条件下水解和缩聚形成整块透明的干凝胶。随后Graham研究发现SiO2凝胶中的水可以被有机溶剂置换,此现象引起了许多化学家的注意。经过科学家的长时间探索,逐渐形成了胶体化学学科。在20世纪30~70年代,矿物学家、陶瓷学家、玻璃学家分别通过溶胶-凝胶法制备出了相图研究中的均质试样,在低温下制备出透明的PUT陶瓷和Pyrex耐热玻璃。其中,在20世纪30年代,Berger和Geffcken首先证实用这种方法即金属醇盐的水解和胶凝化可以制成氧化物薄膜。1969年Bchroder指出,除了SiO2以外,Al、Zn、Ti、Zr、Sn、Pb、Ta、Cr、Fe、Ni和Co的氧化物涂层都能稳定得到。1971年,德国的Dislichl报道了关于溶胶-凝胶法低温合成多组分氧化物玻璃的详细工艺情况,即通过金属醇盐水解得到溶胶,经胶凝化,再于923~973K和200N压力下处理,制备了SiO2-B2O3-Al2O3-Na2O-K2O多组分玻璃。1975年,Yoldas和Yamane等仔细地将凝胶干燥,制得了整块陶瓷材料及多孔透明氧化铅薄膜。20世纪80年代以来溶胶-凝胶技术在玻璃中得到了成功的应用。例如,从1981年开始的几次“以溶胶-凝胶法制备玻璃和玻璃陶瓷”的专题讨论的进行,都进一步引起了人们对溶胶-凝胶法制备玻璃的研究、应用开发的热情。现在,在这个领域的研究活动几乎以爆炸式的速度向前推进,由数人参加的研究小组已达数百个,几乎每个月都有重大进展报道。尤其是在整个无机非金属材料领域,溶胶-凝胶法显示了巨大的优越性和广泛应用的前景。溶胶-凝胶法得到的薄膜具有良好的均一性、高纯度、低合金温度,所以在玻璃、薄膜、涂层等方面得到了成功应用。
溶胶-凝胶技术经过20世纪80年代的理论探讨与90年代的应用研究,已从聚合物科学、物理化学、胶体化学、配位化学、金属有机化学等有关学科角度探索而建立了相应基础理论,应用技术逐步成熟,应用范围不断扩大,形成了一门独立的溶胶-凝胶科学与技术的边缘学科。
2.4.2 溶胶-凝胶基本原理和工艺
溶胶-凝胶是一种通过溶胶-凝胶转变过程制备玻璃、陶瓷以及一些其他无机材料或复合材料的工艺。一般来说,易水解的金属化合物,如氯化物、硝酸盐、金属醇盐等都适用于溶胶-凝胶工艺。关于溶胶-凝胶法的定义范围有两种不同的看法,有人认为溶胶-凝胶过程包括液体溶液、硅胶、金属酸、金属氯化物等胶体悬浮液和金属醇盐溶液中所有的凝胶生长过程。定义的关键是过程中有凝胶生成,而不强调凝胶生成的过程中是否形成了溶胶。而一些人则认为溶胶-凝胶技术应体现出溶胶的性质,溶胶-凝胶技术指的是采用金属氧化物等的溶液制备胶态溶液,在加入稳定剂和调节剂的条件下控制凝胶过程。溶胶-凝胶技术还包括凝胶的干燥和煅烧过程。现在,一般的看法倾向于前者的观点,认为溶胶-凝胶技术的特点在于凝胶的形成,而不在于是否经过了溶胶的过程,但本节仍将溶胶的有关情况予以介绍。
2.4.2.1 溶胶
溶胶是一种特殊的分散体系,它是由溶质和溶剂所组成的亚稳定体系,其中的溶质离子又称胶粒。胶体粒子具有双电层结构,形状很复杂,胶核及其周围电量相等的反号离子使胶粒具有电中性,聚集态胶粒和非聚集态胶粒分别是树枝状和球状。
形成溶胶的方法首先是制备胶体粒子,或者使用机械研磨,使固体细到胶粒大小。制备溶胶的原料主要是无机盐和有机醇盐两类。无机盐适合工业生产,有机醇盐适合精细材料制备,用途不同,选材各异。由金属盐类合成溶胶,存在着两种化学反应机理。首先是水解-缩聚反应,其次是沉淀-胶溶反应。
2.4.2.2 凝胶
凝胶是通过溶胶的胶凝作用或胶凝反应得到的,是一种由细小粒子聚集成三维网状结构和连续分散相介质组成的具有固态特征的胶态体系。溶胶向凝胶的转变过程可简述为:缩聚反应形成的聚合物或粒子聚集体长大为小粒子簇并逐渐连接为三维网状结构。因此可以把凝胶化过程看做是小的粒子簇之间相互连接而成为连续的固体网络。溶胶变成凝胶,伴随有显著的结构变化和化学变化; 参与变化的主要物质是胶粒,而溶剂的变化不大。
凝胶的分类方法按其可逆性分为可逆凝胶与不可逆凝胶; 按力学性能分为弹性凝胶和非弹性凝胶。非弹性凝胶,有时又叫刚性凝胶或不可逆凝胶,这类凝胶经干燥后,再置于热水溶剂中,不像可逆凝胶那样具有变成溶胶的特性。胶凝过程可用结构的变化来表示,溶胶与凝胶结构完全不同。溶胶中的固相粒子能在溶剂中自由运动; 而凝胶中的固相粒子已按一定的网状结构被固定而不能自由移动。从宏观上看,溶胶没有固定形状; 凝胶则具有固定形状。溶胶-凝胶法制备薄膜材料时,凝胶膜在干燥过程中,由于溶剂的蒸发和凝胶的收缩导致应力的产生。研究表明薄膜应力K1与膜厚d存在如下关系: K1=d0.5。薄膜厚度越大,其内应力越大,薄膜内部能够储存一定量的弹性应变能,对裂纹的扩展起到抑制作用,当薄膜较薄时可以保持形态的完整,当膜过厚,产生的应力超过其应变能时,就会造成薄膜的开裂和剥落。除了严格控制一次成膜的厚度外,解决薄膜在干燥过程中的开裂问题常采用以下方法:
①严格控制干燥速率;②增强凝胶骨架、使凝胶内部孔结构均匀化;③降低液相表面张力。
目前普遍认为,除去表面张力对凝胶的破坏作用最有效的办法,是在超临界流体条件下驱除凝胶中的液相,以及在溶胶中添加控制干燥的化学添加剂和改性剂,保持溶胶的稳定性。
2.4.2.3 溶胶-凝胶法的工艺过程
采用溶胶-凝胶法制备无机材料的过程分为以下几个关键环节:①溶胶制备;②溶胶的凝胶化;③凝胶陈化;④凝胶干燥;⑤干凝胶的煅烧和烧结。
(1)溶胶制备
溶胶化过程,在溶液中,溶质和溶剂发生溶剂化、水解或醇解反应,反应生成物聚集成直径1nm左右的粒子并形成溶胶,基本反应如下:
水解:
M—OR+H2O M—OH+ROH (2-45)
通常缩聚具有以下两种途径。
①氧桥合作用(oxolation):
M—OH+M—OX M—O—M+XOH(其中X=H或R) (2-46)
此反应释放出副产物水或醇。在低于化学计量比的水解条件下,主要形成醇,反之则主要形成水。
②羟桥配聚作用:
M—OH+M—OX M—(OH)2—M (2-47)
(2)凝胶化过程
凝胶化是指溶胶化的粒子由于化学键合的作用而聚集长大成为具有三维网状结构的较大分子的过程。凝胶化现象有两种解释。一种是经典的Flory和Stockmeyer理论,其依据是形成凝胶的临界条件是Pc=1/(f-1),式中f为某单体的功能团数;Pc为要形成无限大分子所可能生成的全部键中的部分键分数,在单体聚合生长过程中不生成封闭圈环结构。另一种是穿透理论,其不同之处在于不排除在凝胶化时生成封闭圈环结构的凝胶体。
为防止在液相反应时发生团聚,常用化学表面改性的方法,如加有机螯合剂、表面活性剂及有机添加剂改性,降低粉末表面能,增加胶粒间静电排斥,或产生空间位阻作用而使其胶体稳定。
(3)凝胶的陈化
在陈化过程中,凝胶粒子也可能溶解再沉淀,由于正曲率表面的溶解度大于负曲率表面,导致圆粒表面溶解,表面逐渐平坦,同时凝胶变硬,强度增大,需要注意的是,在不同介质中陈化时,得到的凝胶的结构不同。
(4)凝胶的干燥
凝胶干燥时,包裹在胶粒中的大量液体要排出,凝胶同时收缩,在干凝胶中留下大量的开口和闭口气孔,在凝胶干燥过程中表现出收缩、硬固,同时产生应力,并可能使凝胶开裂,为防止凝胶干燥过程中分体团聚,需要特殊的干燥技术。
(5)煅烧和烧结
由于干凝胶结构中不但含有部分烷氧基或无机阴离子盐,而且它是无定形、非晶体结构,因此必须经过煅烧除去杂质并获得需要的晶体结构。例如氧化锌涂层转变成具有纤锌矿相结构。为了制得致密涂层,干凝胶煅烧后仍须进行烧结。煅烧温度取决于凝胶的孔结构。
溶胶-凝胶的全过程如图2-28所示,由金属醇盐、溶剂、水以及催化剂组成均相溶液,由水解缩聚而形成均相溶胶;均相溶胶经过进一步陈化成为湿凝胶1;湿凝胶经过蒸发除去溶剂或直接蒸发分别得到气凝胶2或干凝胶3,后者经烧结得到致密的陶瓷体4;同时,均相凝胶可以在不同衬底上形成涂膜5,经过焙烧等热处理可得到均匀致密的薄膜6;也可以经过拉丝,得到玻璃纤维7;还可经不同方式处理得到粉体8。

图2-28 溶胶-凝胶的处理过程
不同溶胶-凝胶过程的特征见表2-12。
表2-12 不同溶胶-凝胶过程的特征

2.4.2.4 溶胶-凝胶技术的特点
溶胶-凝胶过程是制备材料的一种新的化学手段,其本质是在材料制备的初期,通过化学途径对材料的化学组成和微观的几何构型进行有效的控制。在无机材料制备领域,溶胶-凝胶技术的应用已对材料的结构和性能产生了巨大的影响,显示出无与伦比的优越性。
(1)优点
①工艺过程简单,不需要昂贵的仪器。
②主要是利用溶液中的化学反应,原料可在分子水平(或原子水平)上混合,可实现材料化学组成的精确控制,尤其是使微量掺杂变得容易。可以合成高均匀性多组分凝胶,在制备复杂组分材料时,能达到极高的均匀性。
③可控制凝胶的微观结构,可对于凝胶的密度、比表面积、孔容、孔分布等进行调节。
④热处理温度低。由于溶胶-凝胶法制备的凝胶前驱体具有高度的均匀性和特殊的微观结构,使后续的热处理在很低的温度下进行。
⑤可以合成通过传统方法得不到的材料。如在制备复杂的氧化物,如高锝氧化物超导材料的合成中具有极大的优势。
(2)缺点
①凝胶化、干燥、热处理很费时间,在制备薄膜时需多次涂覆,间歇操作且过程周期很长。
②产物中往往含有较多的水分和有机物,在干燥和热处理阶段失重较多,易发生破裂。
③若烧成不够完善,制品中会残留气孔以及OH-或C,后者会使制品带黑色。
2.4.3 影响溶胶和凝胶工艺的主要因素
溶胶-凝胶法应用的关键是溶胶的制备,溶胶的质量直接影响到最终所得材料的性能,因此,如何制备满足要求的溶胶成为人们研究的重点,以醇盐为基础的溶胶-凝胶过程的化学反应很复杂,在溶胶、凝胶形成过程中,这些反应可能同时进行,并进一步反应形成聚合物,随着水解的深入,溶胶聚合物的聚合程度加大,最终导致凝胶的生成,结构上表现为空间网络状聚合物的形成,网络空隙中包裹着溶剂分子及反应副产物。溶胶-凝胶技术的关键首先是必须获得稳定的溶胶,其次是在凝胶形成的过程中有效地控制水解缩聚反应。影响溶胶和凝胶质量的因素主要有以下几个方面。
(1)水解度
一般将溶液中水和金属有机物的摩尔比[H2O/M(OR)n]定义为水解度,表示水的相对含量。对于已经配好的溶胶,随着水解程度的增加,成胶时间缩短。这是因为在水解反应中,M(OR)n中的一个OR基团被OH-取代后,剩余的OR基团的反应活性低于首先被取代的OR基团; 而当水量不足时,水解速率缓慢并且水解程度不完全,就生成水解度很低的产物(RO)n-1 M-OH,然后再聚合成(RO)n-1 M-O-M(RO)n-1; 当水解度进一步增大时,可以得到如下的链状聚合物: (RO)n-1 M-O-[M(OR)n-2]x-O-M(OR)n-1;当水解度增加到一定程度,水解反应与缩聚反应速率相当,以致填充整个容器,形成透明溶胶; 但当水解度继续增大时,水解反应加快,形成一些形体不一的大粒子簇,凝胶透明度降低; 当水过量时,水解反应十分迅速而且彻底,生成较大颗粒,进而生成沉淀。加水量少易形成低度交联的产物,使溶胶黏度增大;加水量多则易形成高度交联的产物,使黏度下降。因此加水量对醇盐水解缩聚产物的结构和溶胶的黏度及凝胶时间有重要影响。
(2)溶胶浓度
在溶胶-凝胶形成过程中,溶剂起分散、均化作用。为使溶质充分溶解,首先要求有一定量的溶剂,因而存在一个最大临界浓度。在此浓度以下,其他条件相同时,随浓度的减小,由于单位体积内粒子数目减少,导致粒子间碰撞机会减少,聚合速率减慢,从而延长了胶凝时间。这种情况下形成的溶胶,其三维网状结构的孔洞较大,网络中包裹有大量溶剂及反应副产物,这样使光散射增强,凝胶透明度变差。低浓度溶胶的黏度小,不易形成连续薄膜; 浓度过大,因其大的黏度及表面张力易导致膜面的分布不均匀。因此,应事先选择好欲配制溶胶的浓度。
(3)温度
水解温度高对加快醇盐的水解速率有利,但温度过高,又会产生沉淀。因此水解温度与凝胶的形成关系密切。温度对凝胶形成过程的影响主要表现在成胶时间上,升高温度加快了挥发组分的挥发,同时也加快了分子间的聚合反应,因此,温度升高,成胶时间将缩短。另外,较高温度下也会使某些常温下难以进行的聚合反应成为可能,会影响凝胶质量。
(4)催化剂
由于各种金属离子本身性质的差异,导致其水解速率不一样,有些金属离子的水解非常迅速,很快生成沉淀,这时可事先加入某些有机物来延缓水解速率快的金属醇化物的水解,从而实现对水解反应的控制。由于催化机理不同,对醇盐进行水解缩聚、酸催化和碱催化往往产生结构和形态不同的水解产物。因而选择适宜的催化剂十分重要。
2.4.4 溶胶-凝胶法制备薄膜的常用方法
采用溶胶-凝胶工艺很容易对所制备的氧化物薄膜进行定量可控掺杂,工艺过程简单,无需任何真空条件和复杂设备,可以在任意形状的基底上制备薄膜,并且采用溶胶-凝胶工艺制备的薄膜含有众多分布均匀的微孔,这使得其比表面积大大增加,并且透气性极好。在薄膜制备方面,溶胶-凝胶工艺比其他传统工艺有极大的优势,溶胶-凝胶工艺制备薄膜常用的方法有浸涂提拉法、旋涂法等。
2.4.4.1 旋涂法
旋涂法是在旋转涂覆机上进行的,将基片水平固定于转台,然后将所要涂覆的溶液滴在基片的中央,由旋转运动产生的离心力使溶液由圆心向周边扩展形成均匀的液膜,在一定条件下形成凝胶膜,经过干燥和焙烧得到氧化物薄膜。它是适合涂覆小圆盘和透镜的涂覆方法,因为没有边缘扰动,形成的膜非常均匀。进行旋覆时,流入水平基板表面的溶液或溶胶非常均匀地逐周扩展,再与潮湿空气作用,完成水解-缩聚和胶凝化反应;接着进行热处理而在基板表面形成稳定的氧化物膜。但这种方法不经济,因而较少用来生产无机膜。
采用旋转涂覆法时,薄膜厚度除了受到溶胶性质(如浓度、黏度等)的影响外,旋转涂覆机的转速是决定膜厚的另一个因素。要在整个基板表面获得均匀的薄膜,转速的选取就要考虑到基板尺寸的大小和溶胶在基板表面的流动性能(与黏度有关)。如果转速不高,获得的膜层不均匀;但转速提高,一次成膜的厚度变薄,就需要多次反复地成膜。
2.4.4.2 浸涂提拉法
浸涂提拉法是将整个清洗干净的基板浸入溶液中,然后以一定速率平稳缓慢地提拉出来。提拉涂覆的工艺应用范围很广,对于大型涂件来说更为经济。通常大型玻璃的尺寸达3~4m,将其浸入溶胶浴中,然后小心地以恒定速率提升,提升操作应保持平稳且无震动,而且应十分缓慢,借以协调溶剂蒸发和凝胶速率,由于重力和黏度的作用在基板表面形成一层均匀的溶胶膜。实验证明膜厚与基板的垂直提升速率之间的关系为:d=KvZ/3,比例常数K包含所有影响膜厚的其他因素,如溶胶浓度、黏度、表面张力等。研究表明,所有溶液都在浸涂过程末期,垂直基板底边会出现约2~3μm厚的膜区,这是由于液体存在表面张力,沿基板流下的溶胶有一部分由于表面张力的作用会积存在基板下端区域。对于大型涂件来说,这一无用区可在工艺结束后裁掉。对于小型涂件可用滤纸等吸除基板下端的液滴,也可以在溶胶中添加表面活性剂等成分降低表面张力,从而减轻基板下端的积液现象。但无论如何都会造成基板下端区域凝胶膜一定程度上的不平整和不均匀。