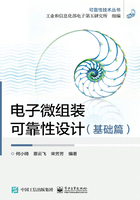
2.3 组件封装技术及材料
2.3.1 模塑封装技术及材料
1.模塑封装技术
在模塑封装中,通常用铜、铜合金或Fe-Ni 42合金(42%Ni含量)制成的金属引线框架来提供芯片的安装表面,也就是芯片的支撑区或黏结区。引线框架还提供了从引线键合区到外部引线或焊盘的电气扇出通路,为了提供可靠的芯片黏结和引线键合,引线框架通常在芯片支撑区和引线键合区的端部局部镀银或金。当完成芯片到引线框架的引线键合后,用热固型(交联)环氧树脂将引线框架-芯片这个组合体包封起来。为了下一级组装的需要,模塑成型后留在模塑料外面部分的引线框架必须加工成最终的形式,并且还需进行引线镀覆。
在模塑产品中所观察到的影响成品率和可靠性的主要问题是电黏性的模塑料流动所引起的冲丝(使引线丝歪斜)和由模塑料中填充料颗粒的尖锐边缘所引起的在器件表面上的局部应力。球形填充料颗粒的使用已降低了芯片表面的微应力。另外,模塑封装中有一种倾向,允许潮气在几天内很快进入器件,各种模塑材料及厚度与潮气渗透率的关系如图2-12所示[2]。在芯片制造中通常所用的铝金属化合物在有潮气、沾污和电场存在的情况下极易被腐蚀。来自构成封装所用的塑料或其他材料的杂质可能使电压阈值偏移或在金属腐蚀时作为电解质。填充料也可影响塑料封装的可靠性和热性能。在改进钝化质量方面器件本身已有了很大的提高,如采用氮化硅和其他膜进行钝化,已使芯片达到“接近气密”的程度。这对防止芯片在模塑过程中受到可能的有害环境侵害是必要的。

图2-12 各种模塑材料及厚度与潮气渗透率的关系[2]
由图2-12可见,通过制样研究,可以预测潮气渗入封装材料(达到外部湿度的50%)所需要的时间,实际上,有机材料的渗透率要比气密封装材料的渗透率高出几个数量级。
2.模塑基封装材料
模塑基封装材料成本低、工艺简单,在电子封装材料中用量最大、发展最快。它是实现电子产品小型化、轻量化和低成本的一类重要封装材料。模塑基封装材料曾经存在致密性不够、离子含量高、耐温性不够等可靠性问题,随着原料性能的提高和配方的完善,这些问题被逐渐解决。目前,需要解决的问题是模塑基封装材料的热膨胀系数与硅晶片不匹配。理想的模塑基封装材料应具有以下性能[14]:①材料纯度高,离子型杂质极少;②与器件及引线框架的黏附性好;③吸水性、透湿率低;④内部应力和成型收缩率小;⑤热膨胀系数小、热导率高;⑥成型、硬化快,脱模性好;⑦流动性、充填性好,飞边少;⑧阻燃性好。
模塑基封装材料多为热固性塑料,主要包括环氧类、酚醛类、聚酯类和有机硅类(硅酮塑料)。常见的有环氧模塑料、硅橡胶和聚酰亚胺等。环氧模塑料由酚醛环氧树脂、苯酚树脂和填充料(SiO2)、脱模剂、固化剂、染料等组成,具有优良的黏结性、优异的电绝缘性、强度高、耐热性和耐化学腐蚀性好、吸水率低、成型工艺性好等特点,封装行业中环氧模塑料占模塑基封装材料的90%以上。
聚酰亚胺可长期耐受200~300℃的高温,具有绝缘性好、介电性能优良、抗有机溶剂和潮气的浸湿等优点,在半导体及微电子工业上得到了广泛的应用。聚酰亚胺主要用于芯片的钝化层、应力缓冲和保护涂层、层间介电材料、液晶取向膜等,特别用于柔性线路板的基材。通过分子设计可以进行材料改性,如提高黏附性,可以引入羟基或环氧基团提高柔韧性、降低固化应力,如引入硅氧键等。目前,在芯片布线光刻领域应用的光敏聚酰亚胺,国内已开始应用。
模塑封装的两个关键要素是选择模塑材料和控制模塑工艺。塑封IC最常用的聚合物是环氧树脂,典型环氧模塑料的成分见表2-2,它由环氧树脂(约占总成分的25%~35%)、硬化剂和固化剂等组成。通常选用酚醛环氧树脂,因为它们具有较高的官能团,有利于改善耐热性。树脂合成时会形成副产品氯化钠,钠离子和氯离子两者对器件的可靠性都是有害的。因此,在树脂被合成为有用的模塑料之前,这些副产品必须从树脂中被仔细地清除掉。
表2-2 典型环氧模塑料的成分

2.3.2 陶瓷封装技术及材料
1.陶瓷封装技术
陶瓷封装技术主要用在需要气密封装的低成本IC芯片和某些混合集成电路封装上,此时封装内部的水平得到有效控制,一般要求内部水汽含量小于5000×10-6/℃,同时气密封装的IC或HIC封装必须通过粗检漏和细检漏试验,以保证在长时间内不会有环境污染和潮气的进入。另外,在封盖之前,封装内的任何沾污都必须得到有效的清除,达到标准规定的控制要求。
在模压陶瓷中使用的零部件需要较少,工艺步骤简单,从而可以使气密陶瓷封装零部件的成本降到最低。这项技术一旦应用条带引线框架(每个条带上有多个封装框架)即可实现自动化生产,因而可以和低成本封装工艺的塑料封装技术形成竞争。对于模压陶瓷封装,器件封装设计者有三种可调控的备选方案,即基本零部件(底座和盖板)、组装部件(已嵌入的引线框架和底座)和称为窗口-框架封装的预加工封装。
为实现高可靠应用的气密封装,由美国MIL-STD-883标准(我国相应的标准为GJB 548)规定的封装漏率定义为“在25℃下,在高压一侧为一个大气压(760mm汞柱绝对值,即101.33kPa)和低压一侧为等于或低于1mm汞柱绝对值(0.13kPa)的情况下每秒通过单条或多条泄漏通道的干燥空气量”,标准漏率单位为atm·cm3/s(即1×105Pa·cm3/s),有关气密封装的粗检漏和细检漏检测程序细节可参见MIL-STD-883方法1014(我国相应的标准为GJB 548方法1014)。粗检漏试验包括管芯渗透和气泡试验,可检漏的范围为10-1~10-5atm·cm3/s;而细检漏试验程序包括氦和放射性示踪方法,可检测的漏率范围为10-4~10-9atm·cm3/s。MIL-STD-883要求气密封装合格漏率试验可通过值为10-8atm·cm3/s,细检漏设备相应的检测灵敏度至少为10-9atm·cm3/s。
模压陶瓷技术使用的原材料为棕黑色的氧化铝(最少为90%Al2O3)陶瓷。为了提高模压陶瓷气密封装的成品率,封装供应商也会提供诸如氮化铝(AlN)、碳化硅(SiC)等陶瓷材料及低热膨胀系数(4.7×10-6/℃)的封接玻璃。
常用封接玻璃的性能列于表2-3,由于陶瓷、Fe-Ni 42合金引线框架和玻璃之间的热膨胀系数失配所引起的母体玻璃中的残余应力和填充料颗粒度分布都会影响机械强度或实现可靠气密封装的能力,理想的情况是封接玻璃应具有低的介电常数、高的机械强度、低的α辐射和较低的封接温度。实际各种封接玻璃都有其优点和缺点,不能达到最理想要求,所以封装设计时需要考虑哪些特性是首要的,并以此为基础进行材料的选择控制。
表2-3 常用封接玻璃的性能

用于嵌入引线框架的封接玻璃介电常数可能会影响引线间的电容及I/O信号通过引线框架的速度。封接玻璃暴露于腔体内,因此,从玻璃填充料中辐射的α粒子可能会影响某些对此敏感的器件的可靠性。
2.陶瓷基封装材料
陶瓷基封装材料相对于模塑基和金属基,其优势在于介电常数低,高频性能好,绝缘性好,可靠性高,强度高,热稳定性好,热膨胀系数低,热导率高,气密性好,化学性能稳定,耐湿性好,不易产生微裂现象。
陶瓷基封装能满足性能要求,但成本相对较高,因此适用于高端微电子器件和组件的封装,如航天、航空等领域,从而达到高可靠、高频、耐高温、气密性强的封装要求。目前使用的典型陶瓷基封装材料有Al2O3、AlN、BeO等,其中Al2O3、AlN陶瓷材料既可作为电路基板,也可作为气密封装外壳材料。
1)Al2O3陶瓷
Al2O3陶瓷基封装材料的特点是综合性能较好,技术成熟,成本低,但相对其他陶瓷基封装材料热导率偏低。Al2O3强度、硬度高,耐热冲击,绝缘性、化学稳定性,与金属附着性良好。电子行业中,Al2O3陶瓷基封装材料约占陶瓷基封装材料用量的90%,在Al2O3中掺入Ag、Ag2Pd等金属导体或低熔玻璃,既可以降低烧结温度,又可以减小介电常数。但是Al2O3陶瓷基材料的热膨胀系数(712×10-6K-1)和介电常数(9.7)比单晶Si高,热导率(17W/(m·K))却相对较低,限制了其在高频、大功率器件和组件中的应用。
2)AlN陶瓷
AlN陶瓷基封装材料的特点是具有较高的导热性能和机械强度,技术较成熟,但成本较高。与Al2O3陶瓷相比,AlN热导率更高,且与Si的热膨胀系数更匹配,介电常数更低,适用于高功率、多引线和大尺寸芯片;AlN陶瓷可以制成多种封装基板并形成封装外壳体;AlN陶瓷的研究重点在于降低烧结温度和提高热导率,以满足大功率器件、组件的应用需求。添加CaF2和YF3助烧剂[15],在1750℃,N2气氛下烧结制得的AlN陶瓷的热导率为180W/(m·K);在510GPa、1300℃下热压烧结50min制得的AlN陶瓷的相对密度达到96.3%[16]。因此为了获得高纯度、高致密的AlN陶瓷烧结体,必须要求原料氧含量较低,形成粒度较小、致密化、强度高的高热导率AlN。就AlN陶瓷基板而言,已研究开发出FP16和LCC64的多层陶瓷封装产品,高温共烧多层陶瓷基板的性能指标如下:热导率150~200W/(m·K);抗弯强度>300MPa;层数7~10;方阻<50mΩ/□;翘曲度<4/5μm/mm[17]。
3)BeO陶瓷
BeO陶瓷基封装材料的特点是具有极高的导热性能和机械强度,以及低介电常数、低介电损耗、封装工艺适应性强等优点,但BeO陶瓷成本高、原料有一定的毒性,限制了它的大量使用。纯BeO陶瓷的烧结温度达1900 ℃以上,常采用Al2O3和MgO等助烧剂降低其烧结温度。BeO陶瓷热导率极高,与金属接近,又是一种良好的绝缘材料,纯度大于99%、相对密度达99%的BeO陶瓷的室温热导率高达350W/(m·K)。BeO毒性大,生产时需采取防护措施,并需要很高的加工温度,这使得BeO陶瓷成本很高并且会污染环境,限制了它的生产和应用。目前,BeO陶瓷基板主要应用于高频、高功率电子器件的散热装置以及航空航天设备等。经金属涂层的BeO基板已用于飞机驱动装置的控制系统和汽车点火装置中。
4)多层共烧陶瓷
多层共烧陶瓷封装材料的特点是可实现高密度布线的封装结构,但成本较高。多层共烧陶瓷基板是由单片陶瓷基板经过叠层、热压、排胶、烧结等工艺制成的。因层数较多,布线密度较高,互连线长度较短,故组装密度和信号传输速度均有提高,可以满足电子系统小型化、高可靠、高效率、高功率的要求,因而得到广泛应用。多层共烧陶瓷分为高温共烧陶瓷和低温共烧陶瓷,其中高温共烧陶瓷主要用于Al2O3、AlN等烧结温度较高的材料,一般温度在1650~1850℃,采用W、Mo、Mn等难熔金属为导线材料。高温共烧陶瓷的优点是强度较高、热导率较高、布线密度较高、化学性能稳定,但高温共烧陶瓷电路互连基板中的W、Mo的电阻率较高,损耗较大。低温共烧陶瓷主要分为三类:微晶玻璃系、玻璃陶瓷系和非玻璃系,采用烧结温度在800~900℃的材料与有机黏合剂按一定比例混合,通过流延工艺制备生瓷带,在生瓷带上冲孔,通孔金属化形成层间的电连接,印刷导体图案,经过叠片、热压、排胶工艺,最后在980℃以下低温烧结,制得多层布线基板。由于烧结温度低,低温共烧陶瓷多层布线基板可与Cu、Ag、Ag2Pd和Au等共烧,介电常数低(615~7121MHz),介电损耗小,热膨胀系数小(513~516)×10-6K-1,并且抗弯强度大(250MPa)、高频性能优异,是高频应用的理想封装材料。
2.3.3 金属气密封装技术及材料
1.传统金属气密封装技术和材料
金属气密封装的作用是保护内部元器件免受外界水汽和污染的影响,一般用于混合集成电路(HIC),主要是保护裸芯片免遭外部环境直接影响而失效。HIC的金属气密封装结构中,金属气密封装外壳一般参照GB/T 15138—94《膜集成电路和混合集成电路外形尺寸》定制,也可根据整机设计要求专门定制;非气密封装有塑封和灌封两种。HIC气密封装工艺,采用钎焊法、冷压焊法、电阻焊法,还有电子束焊、超声焊、激光焊,气密封装后HIC内部水汽含量控制要求小于5000×10-6[18]。HIC封装类别信息列于表2-4。
表2-4 HIC封装类别信息

但是,传统金属基封装材料的热膨胀系数与基板和元器件的热膨胀系数不匹配,界面热应力易导致器件失效。Al的热导率高、密度低、成本低、易加工,但Al的热膨胀系数与Si或GaAs差异很大,因此热应力问题突出,Cu也是如此。柯伐(Covar)合金的热膨胀系数较低,与器件热膨胀系数接近,焊接性良好,但电阻很大且热导率较低,仅用于小功率器件的封装。W、Mo金属的热膨胀系数与Si相近,热导率较高,用于半导体Si芯片的支撑,但W、Mo与Si的浸润性和焊接性差,其表面需要涂覆Ag基合金或Ni,增加了工艺成本,降低了可靠性;另外,W、Mo成本高,影响了产品的大量使用。
由于传统金属基封装材料存在缺点,研制新型金属基封装材料要具有合适的热膨胀系数,还需轻质高强、导热性能高。开发的新型封装材料为Si/Al合金、SiC/Al合金、Cu/C纤维封装材料、Cu/ZrW2O8(TiNi)负热膨胀材料等。
2.新型金属气密封装技术和材料
1)Si/Al合金
近年来,国外利用喷射成形技术制备出Si质量分数为70%的Si2Al合金,其热膨胀系数为(6~8)×10-6K-1,热导率大于100W/(m·K),密度为214~215g/cm3,可用于微波线路、光电转换器和集成线路的封装等[19]。在Si2Al(含硅量50%~70%)合金制备方面也取得了突破,使其具有均匀性好、各向同性、低热膨胀系数、低密度、高热导率等性能特点;加工性能和封装工艺性能良好;环境友好,易于循环使用。
2)Cu/C纤维封装材料
C纤维的纵向热导率高(700W/m·K),热膨胀系数很小(7×10-6/℃),因此Cu/C纤维封装材料具有优异的热性能。C纤维连续分布的铜基封装材料,其热导率受C纤维含量的影响,而且呈各向异性。Cu/C纤维封装材料纵向和横向的热导率差别很大,其热膨胀系数也在纵向和横向间存在显著差别,另外Cu/C纤维封装材料的界面结合是以机械结合为主的物理结合,界面结合较弱,其横向剪切强度仅为30MPa。所以,Cu/C纤维封装材料的弱点是界面强度问题和高成本问题[20,21]。
2.3.4 陶瓷基、模塑基和金属基封装材料比较
典型电子封装材料的性能比较见表2-5。由表2-5可知,陶瓷基封装材料的密度较小,热导率较高,热膨胀系数匹配,是一种综合性能较好的封装方式;模塑基封装材料的密度较小,介电性能较好,热导率不高,热膨胀系数不匹配,但成本较低,可满足一般的封装要求;金属基封装材料的热导率较高、强度高、气密封装效果好,但热膨胀系数不匹配,成本较高,适用于特殊用途的高端产品封装。
表2-5 典型电子封装材料的性能比较
